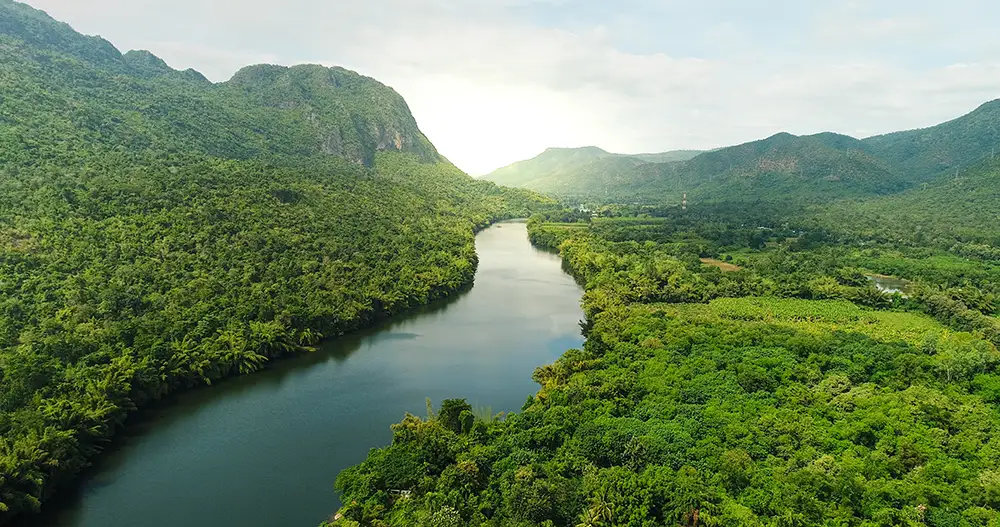

Environmental Sustainability.
Environmental sustainability is embedded in how we do business.
We create value by making sustainability an important consideration of how we design superior products and services. Climate, Waste, Water, and Nature are where we can have the greatest impact.
Our Strategy
We seek to deliver Environmental Impact at three levels: reducing our own impact, helping consumers to reduce their impact, and helping scale solutions across industries.
Our Focus
We create value by making sustainability an important consideration of how we approach our business across four science-based pillars.
Reducing Our Impact
Our sustainability strategy seeks to reduce our own impact across our operations and supply chain. We create value by making sustainability an important consideration of how we design superior products and services through four science-based pillars — Climate, Waste, Water and Nature.
Climate
We are reducing our absolute emissions across our operations, including those from our manufacturing plants and additional facilities. We will balance any remaining emissions from our operations and supply chain by advancing natural or technical solutions that remove an equivalent amount of GHG emissions from the atmosphere.
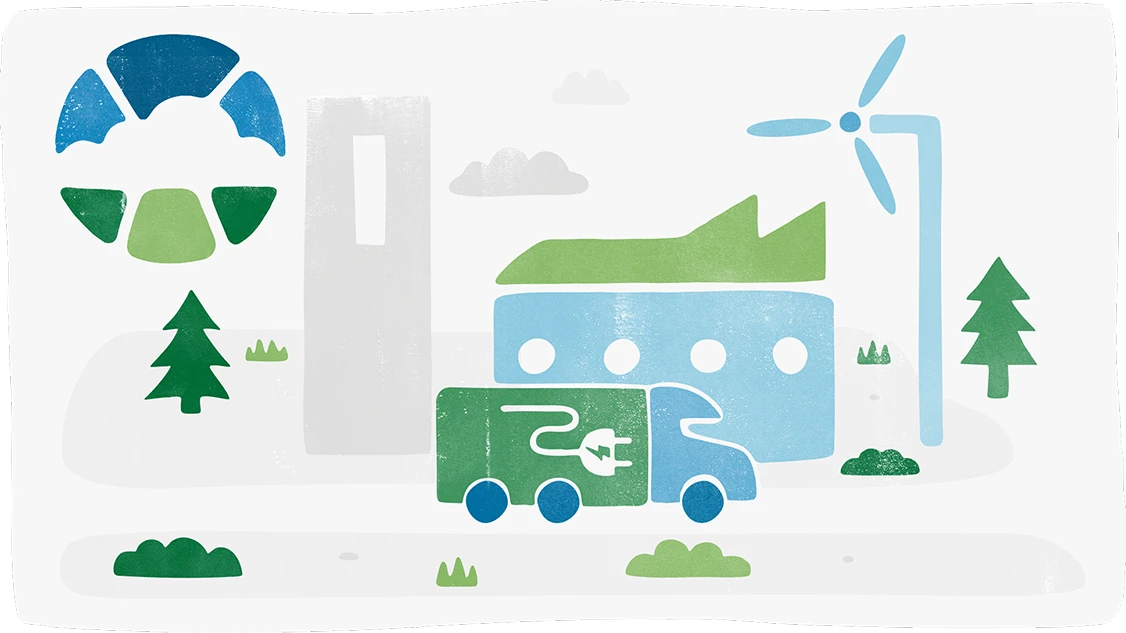
Waste
Throughout our journey we have been working to reduce material usage in operations, reduce our usage of virgin petroleum based plastic resin, and to design our consumer product packaging to be recyclable or reusable.
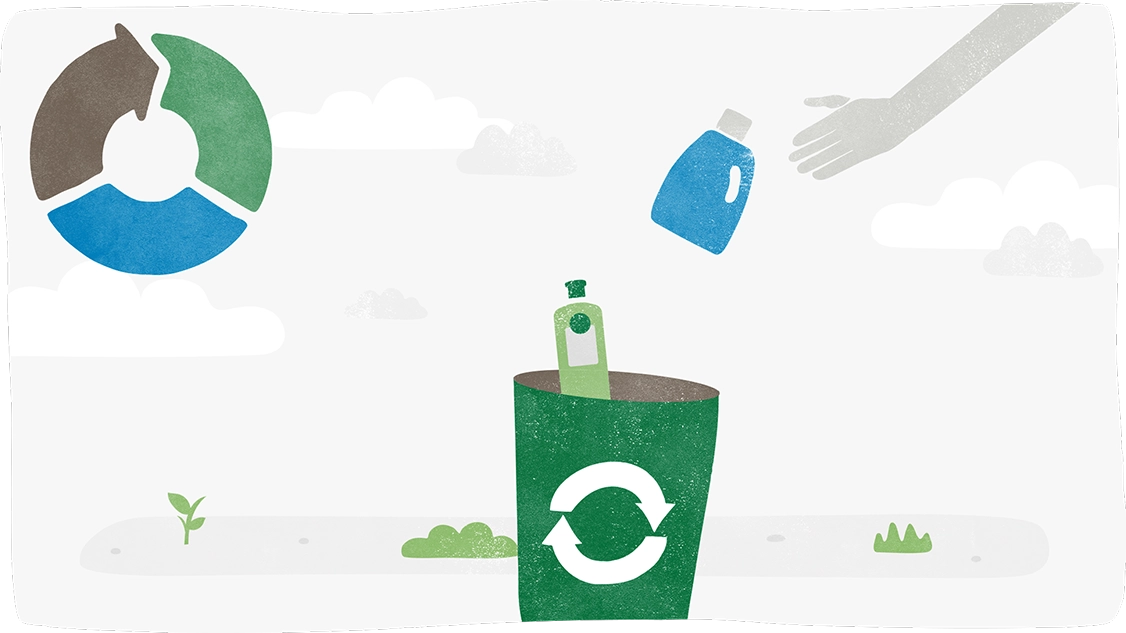
Water
To reduce water use in our operations, our efforts focus on facilities exposed to high water risks. We aim to play our part in protecting the water resources and address the key challenges impacting our operations and the local communities where we operate.
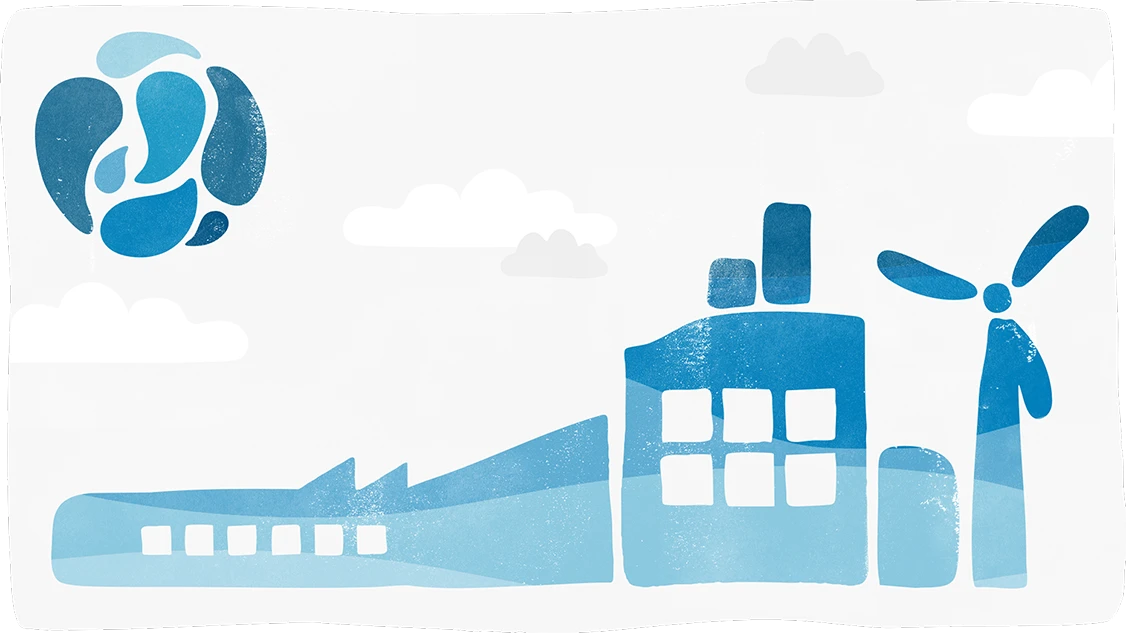
Nature
We are committed to responsible sourcing of key commodities like wood pulp, palm oil and paper packaging together with respecting human, labor and land tenure rights in our supply chains. We partner to help restore and protect landscapes near our existing supply chains and invest in natural climate solutions that can remove and store more carbon.
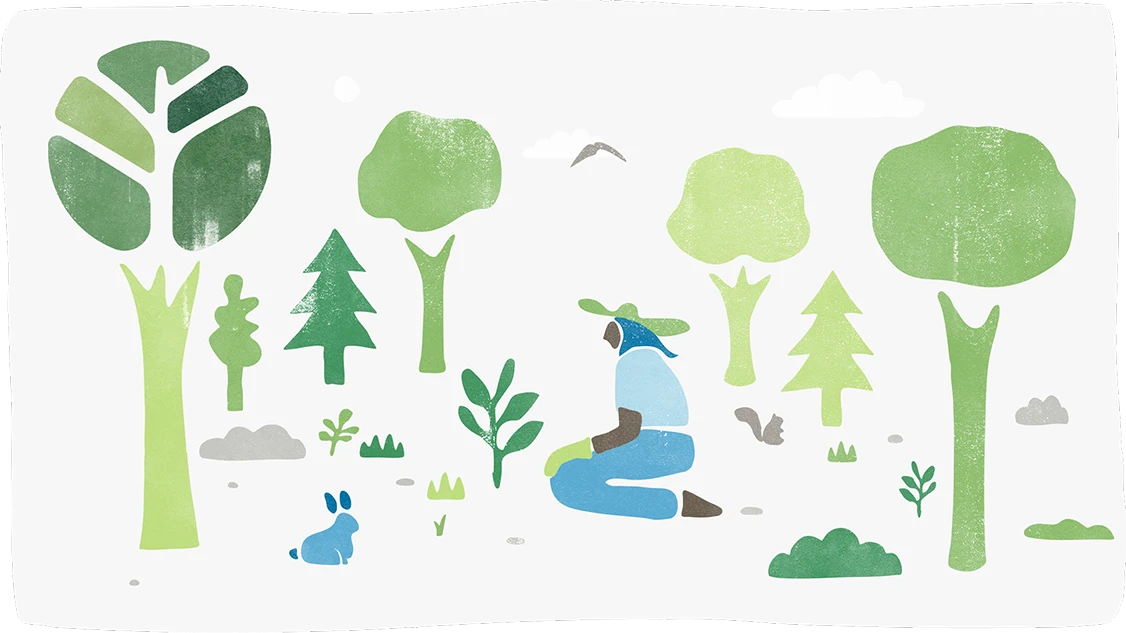
Helping Consumers Reduce Their Impact
Our sustainability strategy seeks to help consumers reduce their impact by making it easier to reduce resources like energy, water, and waste when they use our products.
Scaling industry-wide solutions that reduce environmental impact
Our sustainability strategy seeks to be a catalyst for cross-value chain collaboration. We recognize that scaling solutions across industries is vital and make some of our innovation available so that together we can increase the scope, speed, and spread of change.
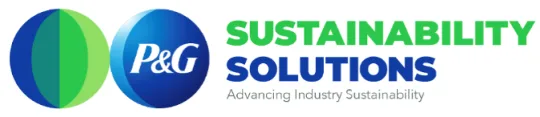
Sustainability Solutions: Technology to Catalyze Industry Progress
Sustainability Solutions by P&G brings together partners and technologies designed to reduce environmental impact across multiple business sectors in the company by being a catalyst for cross-value chain collaboration. We also make some of our innovations available so that together we can increase the scope, speed, and spread of change.
Our Ambitions
Where we can make the biggest difference for people across our operations, supply chain, and the communities we serve.
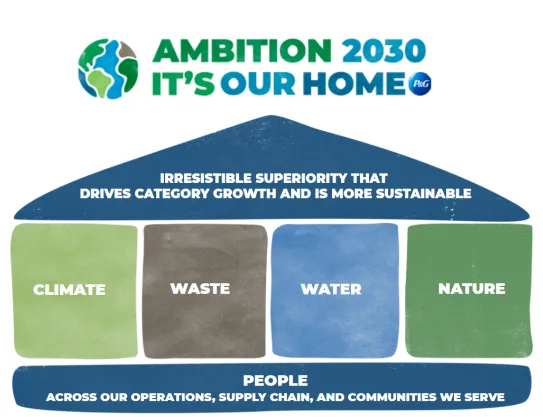
Our Ambition by 2030
P&G’s Ambition 2030 supports our brands’ ability to provide irresistible superiority that is sustainable to improve lives now and for generations to come. Its foundation is improving the livelihoods of people across our operations, supply chain and the communities we serve.
We are working across Climate, Waste, Water and Nature to reduce our impact in our operations, empower people to reduce their impact when they use our products, and scale industry-wide solutions by being a catalyst for cross-value chain collaboration. We cannot achieve these goals alone. This requires collaboration between the private, nonprofit, and public sectors and involves every aspect of our business.
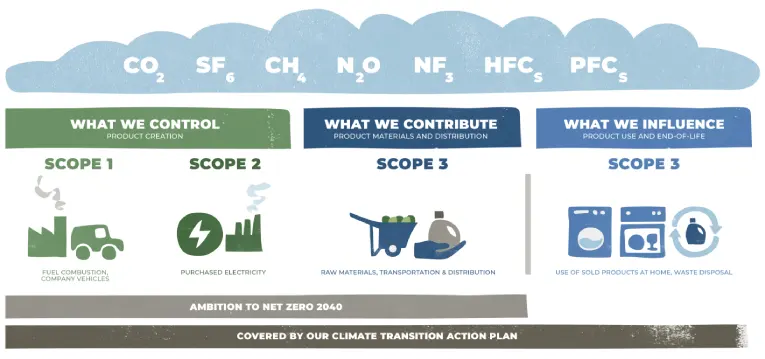
Net Zero by 2040
P&G’s ambition is to reach net zero greenhouse gas (GHG) emissions across our supply chain and operations – from raw material to retailer – by 2040. To help pace our progress toward 2040, we have established near-term science-based Climate targets as part of our Ambition 2030 goals.
Additional Resources and Reports
Climate
Waste
Water
Nature
Frameworks
P&G Policies and Commitments
For more detailed information about our disclosures, policies, and progress, please visit our ESG Portal.